— 9 min read
Value Engineering in Construction: 6 Steps to Increase Project Value
Last Updated May 20, 2025

Every project owner or developer begins a construction project with a version of the same question: How can we achieve the best outcome at the lowest possible price within the shortest time frame? The contractors performing the work approach each job with a similar query: How do we produce work according to the specifications within the available budget, timeline, and resources? For many projects, value engineering can help answer both questions.
Value engineering is a systematic method used to increase project value within the existing parameters and specifications. This article explores value engineering on a construction project, including each of the six steps in the process, roles and responsibilities and how it can improve project outcomes.
Table of contents
The Basics of Value Engineering
Value engineering is a prescriptive process for analyzing project components — such as materials, systems, equipment or features — to find alternatives that produce the same results but provide greater value. Value engineering can help solve problems, reduce costs or improve quality in ways that can lead to positive outcomes for all stakeholders.
The idea for value engineering was pioneered during World War II by an engineer at General Electric named Lawrence D. Miles. In order to address widespread material shortages, Miles developed a new approach to identify and develop low-cost alternatives.
In construction, the process is used to reduce costs without significant compromise on quality or function. However, value engineering is much more than simple cost-cutting. Rather, it is a method employed to increase value, usually by finding alternatives that either improve quality at the same price or maintain quality while reducing costs.
For example, project plans might call for fan-powered boxes that each cost $2,600. Through value engineering, the GC discovers fan-powered boxes with similar specs, but only cost $2,300 each, making them a better value. The process might also reveal alternatives that cost only $1,200 each, but with less power and a shorter lifespan, saving on cost — but dramatically reducing project value.
Factors Considered During Value Engineering
Increasing value on a construction project can be done by considering a few different factors and asking a number of related questions.
Factor | Questions To Ask | Example |
Cost | What’s the price? Does an alternative that costs less perform the same function? | An engineered quartz countertop that matches the color and durability specifications but costs 10% less than quartzite. |
Function | What function does it perform? Can another item accomplish the same result without dramatically raising the price? | A window that costs 3% more than planned but has a special coating that helps with temperature regulation, reducing energy costs during building operation by 6%. |
Longevity | How long is this going to last? What’s the warranty? Is there something that will last longer, saving the owner money in the long run? | Plumbing fixtures that cost 5% more than the ones identified by the design team but offer greater resistance to corrosion in the coastal area. |
Lead time | How long will procurement take? Is there something that won’t take as long to get without compromising quality? | Flooring that costs more per square foot than the alternative but can be procured in a quarter of the time, reducing the schedule by three weeks. |
When Should Value Engineering Take Place?
Most of the time, value engineering happens during planning or preconstruction, because it’s easier to make changes or explore alternatives without delaying the project. An owner might specifically ask to find ways to save money or a general contractor (GC) might discover something on their own that they think can be done cheaper or at a higher quality.
When value engineering happens during the construction phase, it is most commonly in reaction to an unexpected issue.
For example, an owner whose project has incurred an array of unexpected costs might ask the GC to value engineer some of the remaining parts to get the project back under budget. The construction phase is rarely an ideal time for value engineering because changes are more likely to lead to schedule delays.
Value engineering can also depend on the type of contract used on a project. For guaranteed maximum price projects, which say contractors cover any costs beyond a set maximum price, value engineering will happen continuously. For lump sum contracts, which set a fixed budget, much of the value engineering will happen during the bidding process.
6 Steps of the Value Engineering Method
Many engineers gain enough experience in value engineering that they are able to constantly and effortlessly identify areas to save money, accelerate the timeline, or increase quality. Even then, they are still practicing the following six steps, with the same objectives and questions.
Phase | Objective | Key Question |
Information gathering | Collect data about the project or parts, such as cost, specifications, schedule, or owner’s intentions. | What is the goal? |
Functional analysis | Analyze elements to determine their function and necessity for the project. | What does this need to do? |
Creativity and innovation | Develop ideas for alternative ways to achieve the element’s function. | What are other ways to do this? |
Evaluation | Assess the alternative solutions for advantages and practicality. | Does this increase or decrease value? |
Development | Develop promising alternatives by exploring impacts on cost, quality, timeline, and owner expectations. | How does the new idea change project costs, function, and schedule? |
Presentation | Share the most promising alternatives with the owner with clear pros and cons. | What options should the owner consider? |
Roles & Responsibilities in Value Engineering
Value engineering is often prompted by an owner wanting to lower costs or a GC seeing ways to increase value, but the process requires input from many stakeholders.
Owner
- Often prompts value engineering by requesting ways to save money
- Ultimate decision maker: They will be presented with the most promising alternatives and have the power and knowledge of the budget to decide whether an alternative is necessary, beneficial, and, quite simply, if they like it.
General Contractor
- Sometimes identifies the potential for added value
- Usually finds the alternatives, either by going to vendors, subcontractors, or searching online for differences in price and quality
- Presents alternatives to the owner and helps them consider the possible benefits
- Responsible for the executing on the final decision
Design Team
- Approve potential alternatives after assessing for safety, performance, and aesthetics
- Collaborate with the GC to provide information, whether sharing construction specs or explaining their vision
- Occasionally find alternatives, if requested by the owner during the design phase
Stay updated on what’s happening in construction.
Subscribe to Blueprint, Procore’s free construction newsletter, to get content from industry experts delivered straight to your inbox.
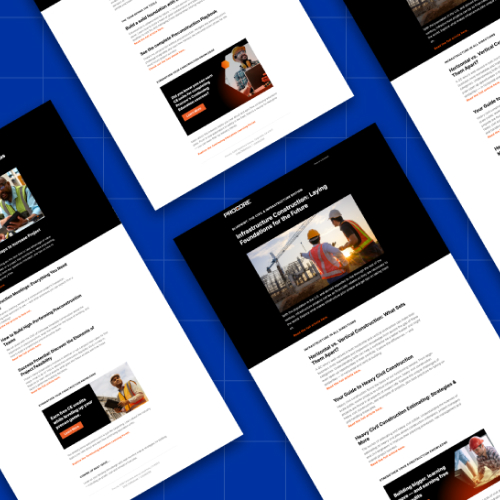
Certified Value Specialist
Large general contractors sometimes have consultants on staff who specialize in finding value in a project. Sometimes, an owner or consulting firm will hire someone with this specialty to monitor a project.
- Reviews all design choices and generates ideas to maximize value
- Communicate with GC about parts and, when necessary, prompt them to find alternatives
- Provide some alternatives
The Benefits of Value Engineering
Value engineering increases value, most commonly by reducing costs, but it has a number of additional benefits:
- Relationship building: For general contractors, value engineering can be a way to build trust with a client and demonstrate their commitment to completing projects under budget and at a high level of quality.
- Better decision-making: Value engineering increases communication, as the GC, design team, and owner are reviewing choices and critically engaging with various potential outcomes.
- Creating contingencies: Value engineering can get a project under budget so that an unexpected issue won’t be as devastating for the budget or timeline.
Value Engineering Best Practices and Potential Challenges
Value engineering can sometimes complicate the construction process by requiring more communication and introducing new considerations. However, there are a few ways to ensure the process stays as effective as possible.
Stay organized.
Keep the budget, schedule and building plans up to date so that potential changes don’t get lost. It can also be helpful to track all potential alternatives on a spreadsheet, as they each have their own specs and costs.
Consult with specialty contractors.
Specialty contractors have a deep knowledge of their trade, including types of material and construction methods. Cultivate a relationship with subs so it’s possible to ask them for ideas or get their feedback on potential decisions. They might be able to help save money by suggesting alternative parts they have used before or save time by suggesting methods they know to be more effective.
Monitor the relationship with the design team.
For general contractors, one of the biggest challenges with value engineering is maintaining a positive relationship with the design team. If a GC pitches a change to an owner, it’s possible for the design team to feel challenged or, even worse, called out for not having considered it in the first place. This can be mitigated by being open and proactively communicating. Call the design team with an idea before going to the owner to ask if the idea could work, aligns with their vision, or is missing anything. An architect or engineer will often feel better and more invested in approving a decision if they are consulted with and brought into the process.
Do research.
Before presenting ideas to an owner, research the changes thoroughly. Being able to knowledgeably present options with a command of the market, lead times, and potential implications for the budget and schedule can save a lot of back and forth.
Don’t overdo it.
Presenting too many options to an owner can lead to delays that are worse than if nothing changed at all. Too many options can be hard to track for the GC, hard to decide between for the owner, and cause the design team to feel that the goal is just to make things cheaply. Even if an owner can make decisions quickly, too many options might push them to unnecessarily try to maximize every little part of the project.
The Future of Value Engineering in Construction
Recent challenges with material procurement have made value engineering more common than ever. The rise of artificial intelligence might create opportunities to quickly and thoroughly search every possible alternative to an element, sorting for price, specs, and lead time.
Regardless of how convenient and thorough the process becomes, the ability to identify ways to maximize value and creatively find ways to execute on them will remain an extremely valuable skill, specifically for owners looking to stay under budget and general contractors looking to deliver high-quality projects.
Was this article helpful?
Thank you for your submission.
100%
0%
You voted that this article was . Was this a mistake? If so, change your vote here.
Scroll less, learn more about construction.
Subscribe to The Blueprint, Procore’s construction newsletter, to get content from industry experts delivered straight to your inbox.
By clicking this button, you agree to our Privacy Notice and Terms of Service.
Categories:
Tags:
Written by
Matt Peter
Matt Peter is a Solutions Engineer at Procore. Prior to joining the construction-software firm, Matt spent five years working as a Project Manager for BIG Construction and Builtech Sevices in Chicago, where he currently resides. He also worked as a Project Engineer for Skanska in Tampa. Matt received his Bachelor of Arts in Economics from the University of Wisconsin-Madison.
View profileJames Hamilton
70 articles
James Hamilton is a writer based in Brooklyn, New York with experience in television, documentaries, journalism, comedy, and podcasts. His work has been featured on VICE TV and on The Moth. James was a writer and narrator for the show, VICE News Tonight, where he won an Emmy Award and was nominated for a Peabody Award.
View profileExplore more helpful resources
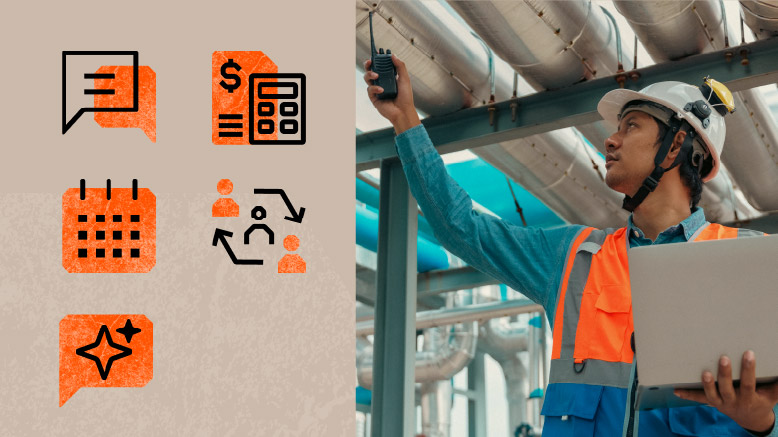
The Top 5 Skills of High-Performing MEP Professionals
Compared to standard MEP professionals, high-performing MEP pros don’t just get the job done. They also combine five key skills around technology, scheduling, finances, communications and flexibility into a proactive approach...
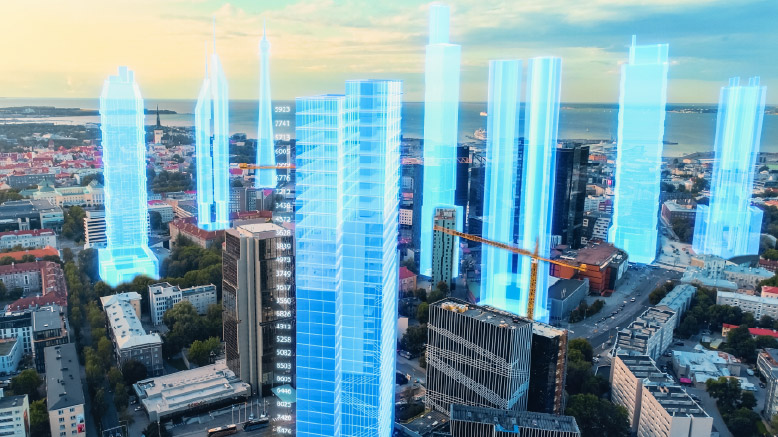
How AI is Reshaping Decision-Making and Project Resilience in Civil Construction
In construction, the ability to make informed, timely decisions is paramount. No longer is it sufficient to rely solely on historical data or reactive problem-solving. Enter artificial intelligence (AI), a...
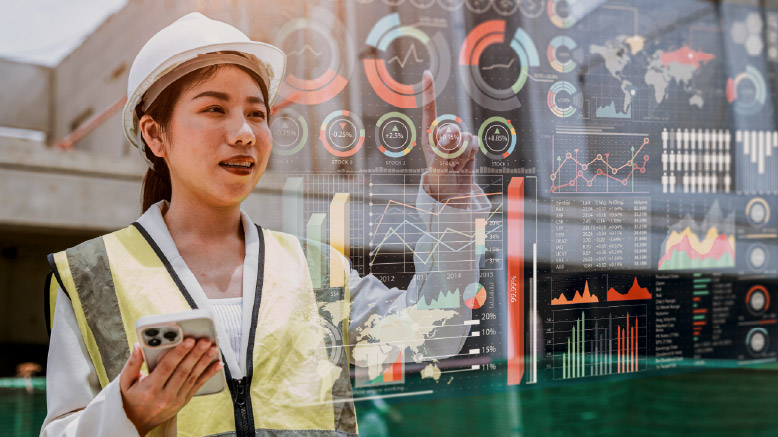
How AI is Redefining Efficiency & Safety in Civil Construction
As demand for new and modernized infrastructure surges, the civil construction industry faces an imperative to deliver projects with unprecedented speed, precision and safety. Emerging at the forefront of this...
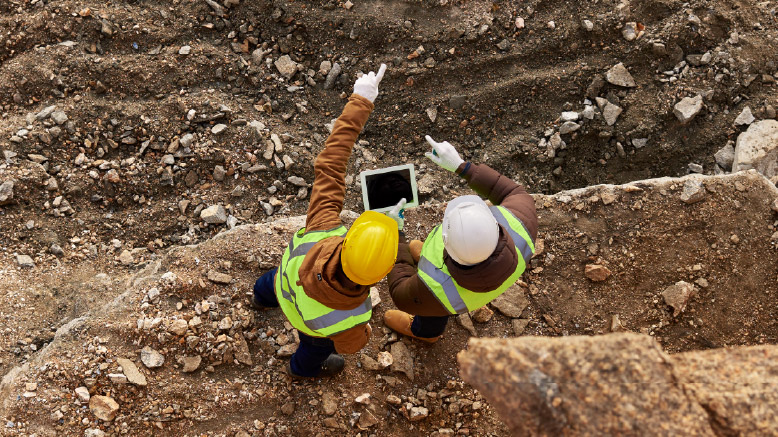
Building a Culture of True Tech Readiness in Civil Construction
While significant investments are pouring into revitalizing the nation’s infrastructure, the true capacity to capitalize on this opportunity hinges on more than just funding — it relies on a fundamental...
Free Tools
Calculators
Use our calculators to estimate the cost of construction materials for your next project.
Templates
Find a template to help you with your construction project tasks.
Material Price Tracker
Get the latest U.S. retail prices and view historical trends for common building materials.
Glossary
Explore key terms and phrases used in the industry.